Marussia F1 team showcases technology used in Formula 1
We go behind the scenes to see 3D printers, ERP systems and a 60 Teraflop Computation Fluid Dynamics Cluster in action at the team's site in Banbury.
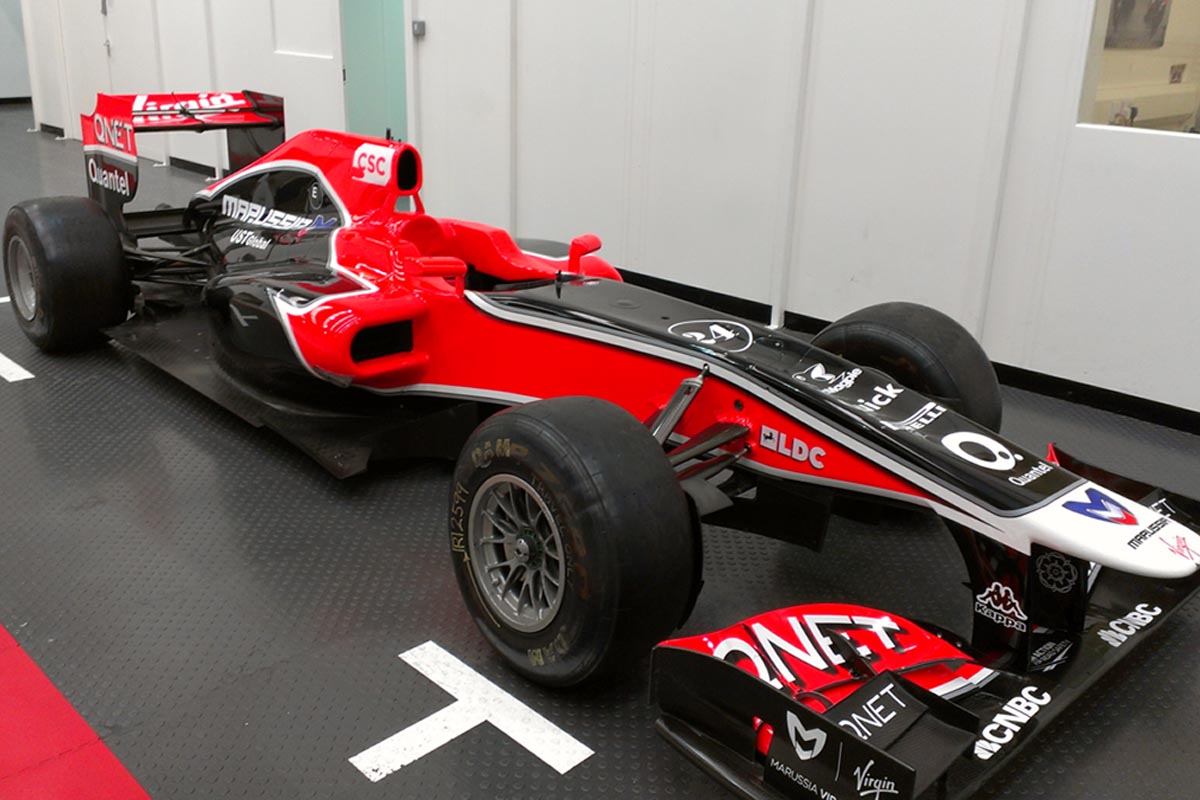
Marussia F1 - 2011 model
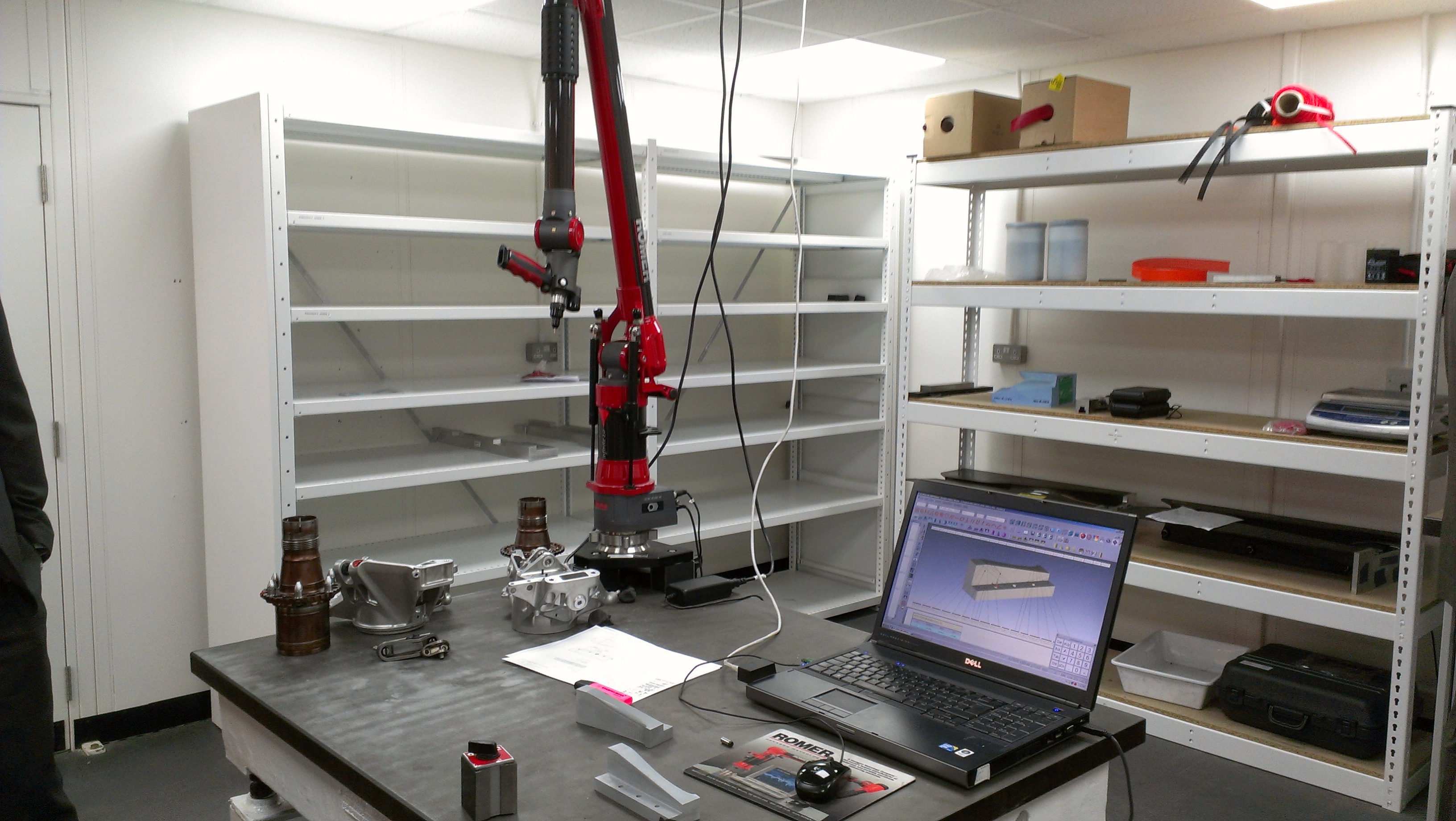
Inspection
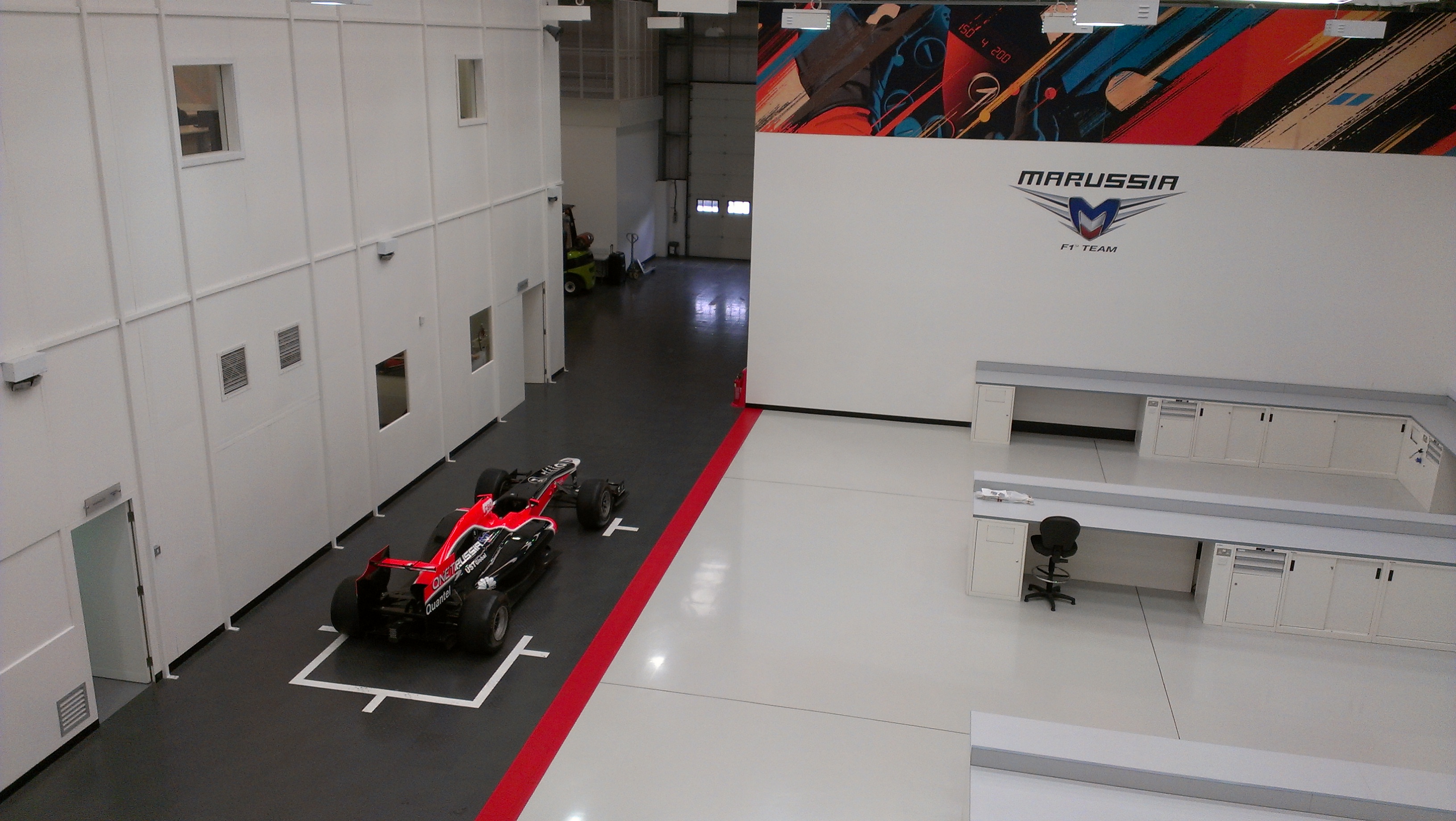
Marussia F1 Garage
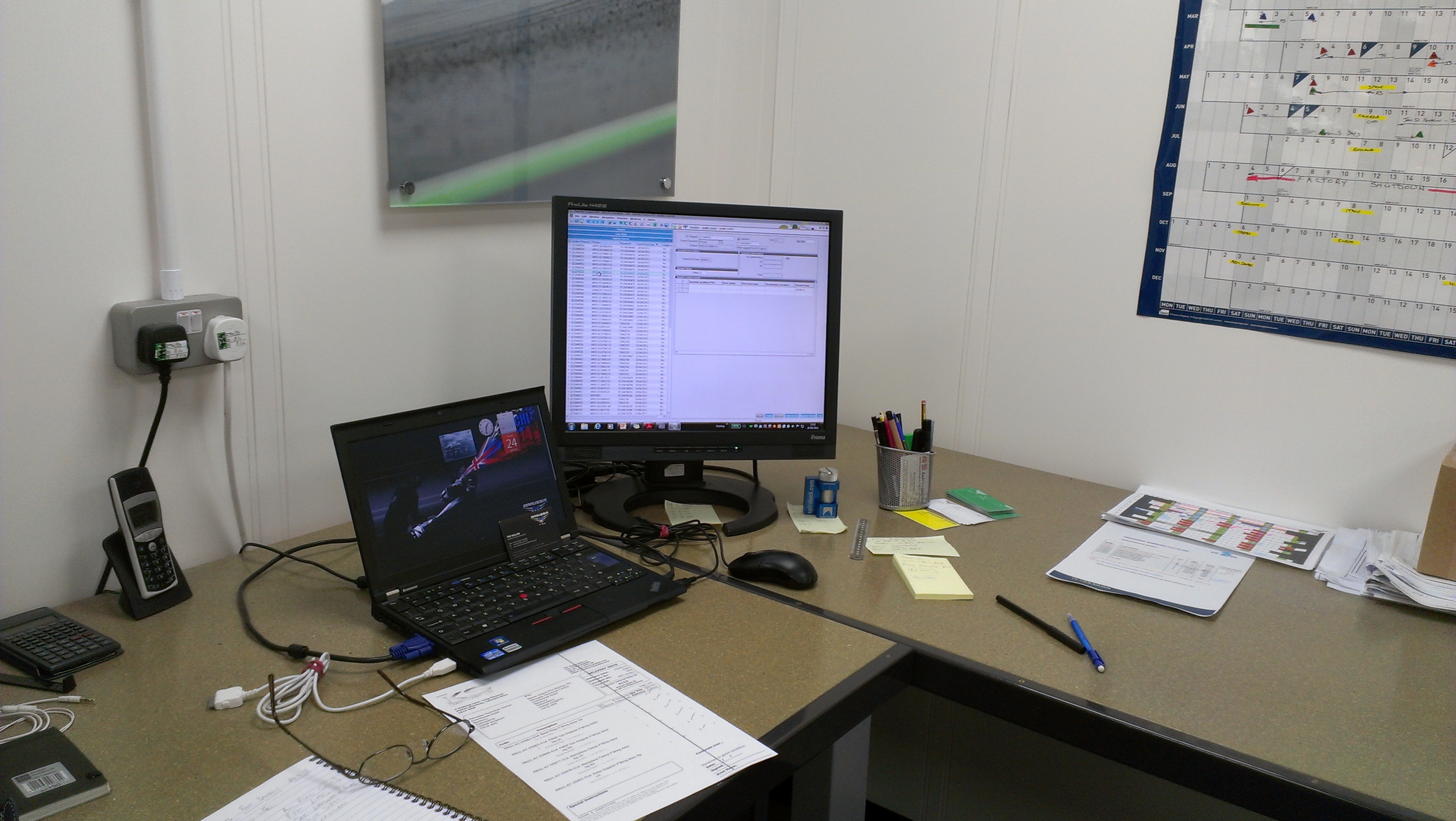
Sage ERP X3
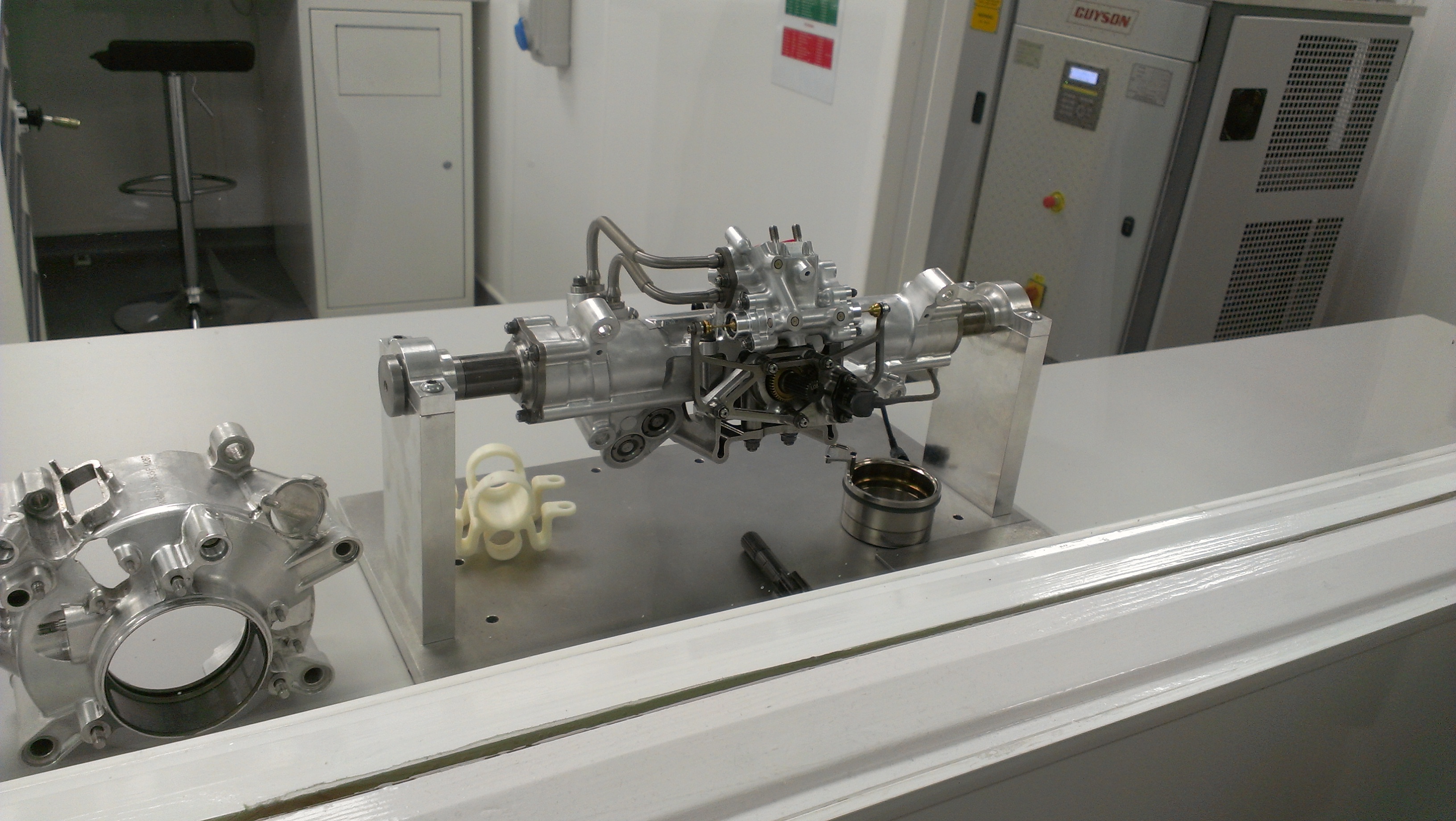
Hydraulics department - dust free
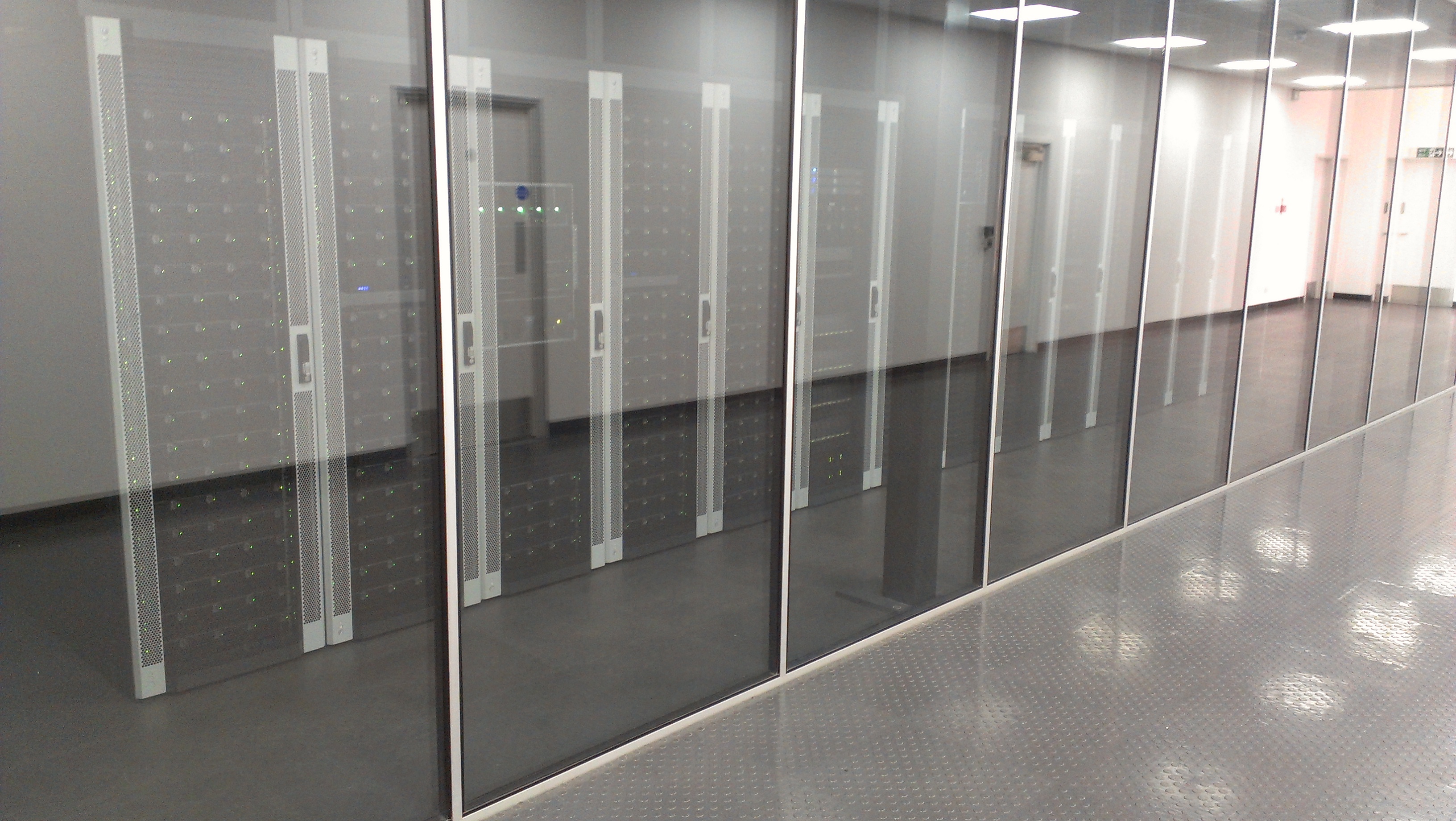
Computation Fluid Dynamics Cluster
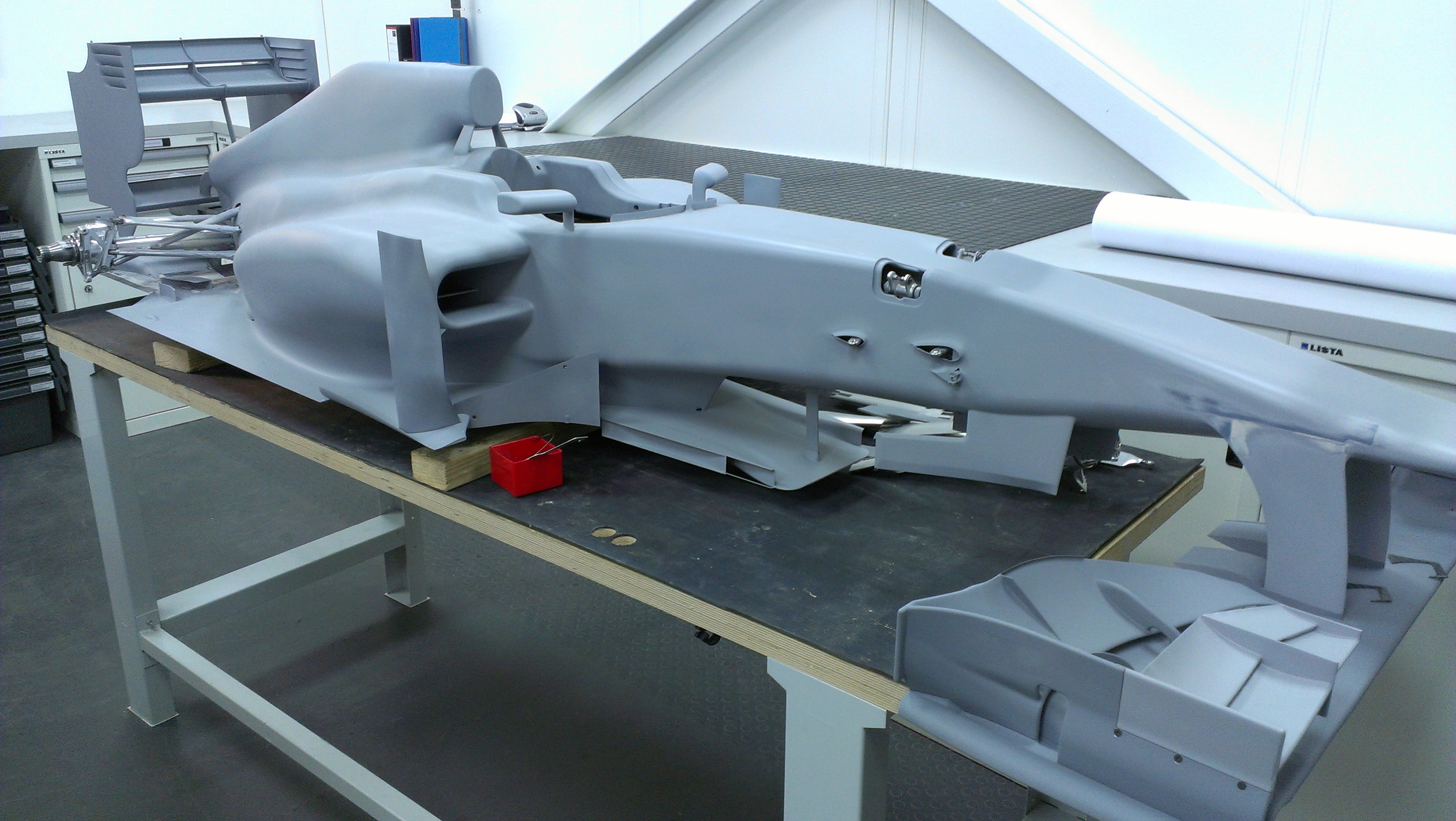
Marussia F1 50 per cent scale model
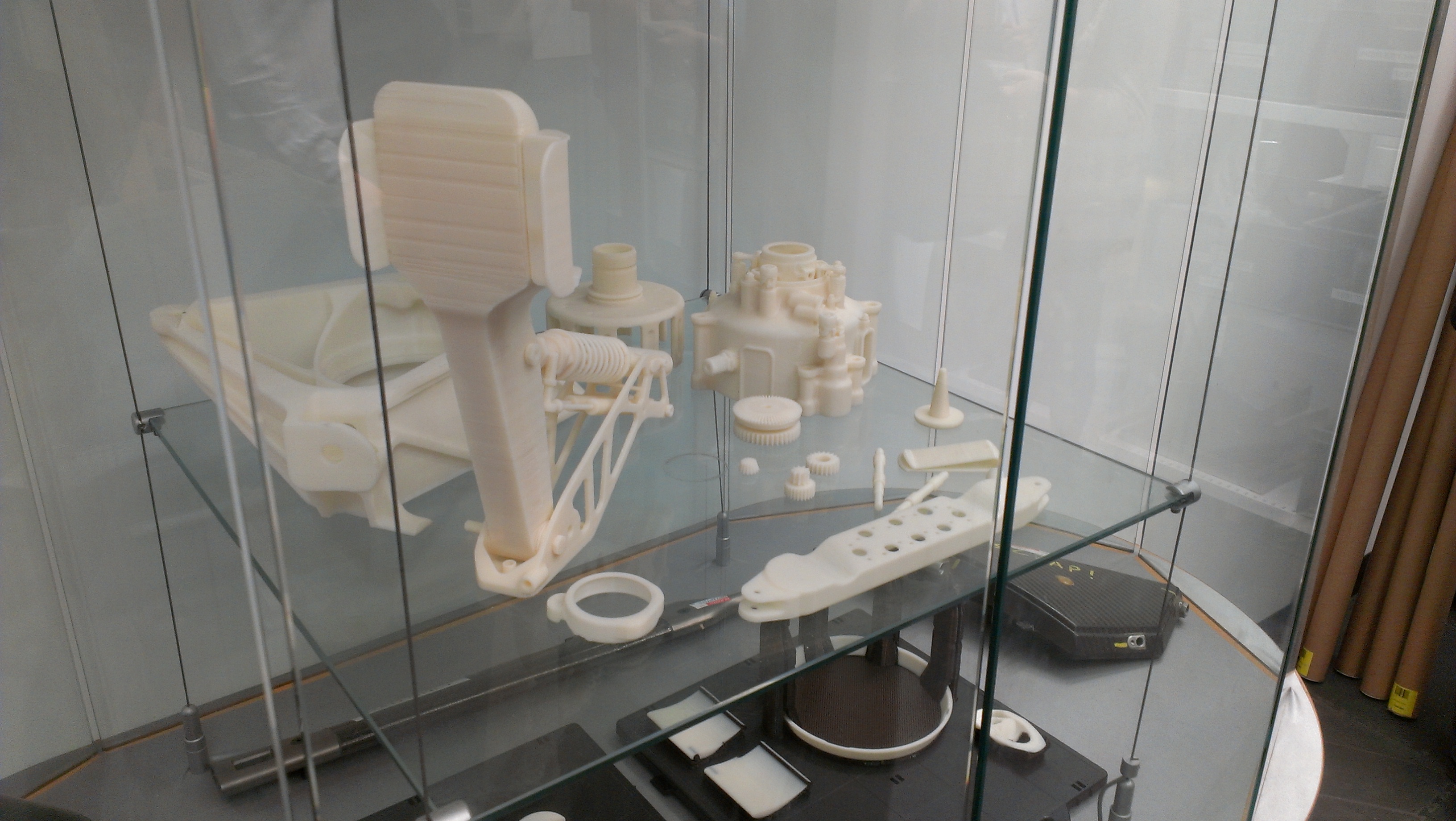
3D models
Formula 1 is all about pushing the boundaries of speed, so it's no surprise technology plays a huge role in building cars, let alone getting them to the end of a race.
The Marussia F1 team uses enormous amounts of technology including 3D printers to build prototype parts, a Sage ERP system to monitor inventory and a mammoth 60 Teraflop cluster to carry out simulations.
Before we delve into the technology, lets get a bit of background about one of the newest teams in the paddock. Marussia F1 debuted back in 2010 under the Virgin Racing banner.
So far the team has a best-placed finish of 14th, in what is considered to be one of the most high-tech and competitive sports in the world.
Kevin Lee, operations director at Marussia F1, has set an ambitious target of achieving a podium place at the inaugural Russian GP in 2014.
We took a look behind the scenes of the company's factory in Banbury to see the effort that goes into building a Marussia F1 racing car.
The team creates prototype parts to ensure they fit together before commissioning them
Get the ITPro daily newsletter
Sign up today and you will receive a free copy of our Future Focus 2025 report - the leading guidance on AI, cybersecurity and other IT challenges as per 700+ senior executives
There are over 4500 parts on each car, but constant enhancements mean this number rapidly increases throughout the season. Lee estimated around a third of the parts on the car change between the first and last race of the year.
Every part is designed in-house and then custom built by a supplier. Marussia F1 does not manufacturer any parts in-house at present, but engineers are able to create prototypes, as seen above. These parts are made using a 3D printer, which builds layers of Resin to create the piece. This process can take around 24 hours, depending on the size of the part.
To keep track of parts, Marussia F1 uses Sage ERP X3. The integrated resource planning system allows employees to carry out purchasing, inspection, inventory control, and keep track of invoices and receipts.
Each part is inspected before it can be used on the car
To ensure reliability, all parts are thoroughly inspected. A measuring probe with an industrial ruby on the end is used to check the tolerance of parts. It is possible to measure up to a Micron (0.001mm), which is smaller than a particle of dust (0.004mm).
Formula 1 car parts are extremely complex. A team of engineers is needed to simply start Murussia's Cosworth engine, which must be warmed for 40 minutes prior to doing so.
-
Should AI PCs be part of your next hardware refresh?
AI PCs are fast becoming a business staple and a surefire way to future-proof your business
By Bobby Hellard
-
Westcon-Comstor and Vectra AI launch brace of new channel initiatives
News Westcon-Comstor and Vectra AI have announced the launch of two new channel growth initiatives focused on the managed security service provider (MSSP) space and AWS Marketplace.
By Daniel Todd
-
Why managing shareholders is key to innovation
In-depth Seeking out investment for new technologies and seeing your ideas through requires continuous and measured trust-building
By Elliot Mulley-Goodbarne
-
How Crew Clothing went mobile to turn around a struggling business
Case Study Mobile sales tech unleashed a tide of change, buoying further growth across the UK coast-inspired casualwear chain
By Fleur Doidge
-
The Total Economic Impact™ of SAP finance transformation services with TruQua
Whitepaper Business benefits and cost savings enabled by accelerating the SAP central finance transformation
By ITPro
-
Avoiding cloud migration pitfalls for SAP
Whitepaper Determining the best approach to SAP HANA
By ITPro
-
What tech investors can learn from three under-fire CEOs
Analysis With clear lessons to learn from the high-profile cases of Autonomy, Theranos, and Wirecard, investors should tread carefully in future
By Rois Ni Thuama
-
What to expect from Oracle CloudWorld 2022
Opinion Larry Ellison and co are heading to Las Vegas for a rebranded cloud-centric show
By Bobby Hellard
-
Acumatica reinforces channel focus with new Services Partner Program
News New initiative will see service partners join the cloud ERP provider’s VARs and ISVs
By Daniel Todd
-
Microsoft announces Teams chat integration for Dynamics 365
News The integration offers features to streamline collaboration between teams while aiming to enable the faster closing of sales
By Daniel Todd