What the supply chain crisis taught us – and how businesses can prepare for the next one
Businesses should expect the unexpected, think beyond natural cycles, and forecast supply-chain challenges
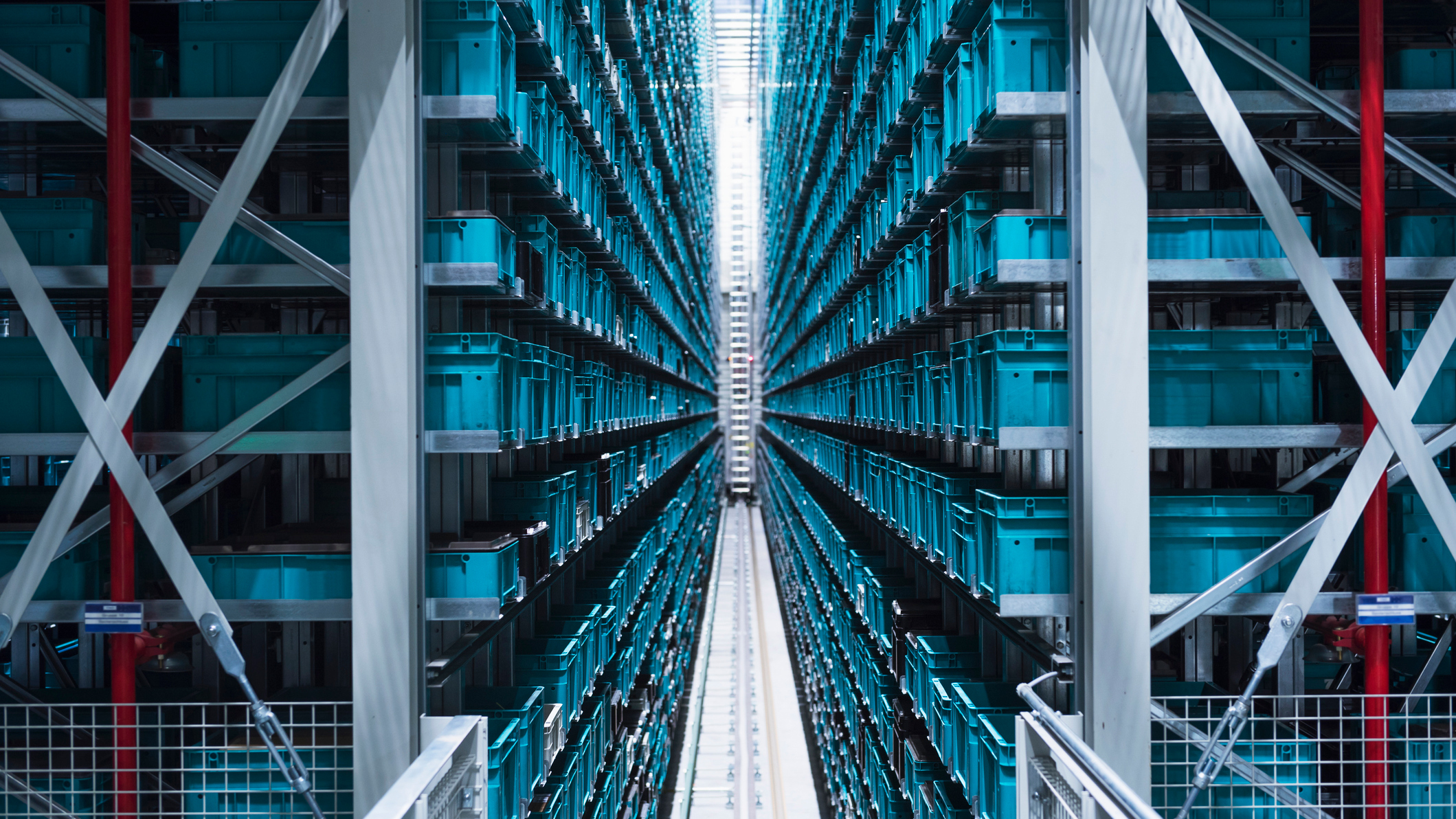
With fresh constraints on the near to medium horizon on aspects of the supply chain from shipping to materials sourcing, the IT industry stands reminded of its vulnerability to global shocks.
In recent years this has been especially apparent, with the lack of diversity in component suppliers and design alternatives laid bare amid the pandemic and wider economic downturns.
Fred Lherault, field CTO, EMEA, at vendor Pure Storage, agrees. Even as Covid shrank in the rear-view mirror, GPU and wider supply constraints are emerging in the wake of massive AI/ML adoption - and that's on top of continued skills shortages and potential IT supply chain challenges around networking power and data transfer needs.
Alternative component options should become common to simplify the engineering side of the supply chain and reduce susceptibility to availability challenges, Lherault says. "We've built flexibility into our supply chain," he adds, noting that typically, however, people don't plan for something unpredictable to happen.
Have we learned from the supply chain crisis?
Rasheed Mohamad, executive vice president for global operations and business technology at Alcatel-Lucent Enterprise (ALE), notes that when businesses spend too long on predictable challenges and optimizing systems for current conditions they can find themselves insufficiently resourced to manage unpredictable events down the line.
"People have tended to make supply chains lean because cost is a big factor. Yet the supply chain has challenges all the time," Mohamad notes.
Therefore it's critical to look beyond simply globally procuring the best quality for the lowest price, building in resilience and enough redundancies and localization to cover your bases when something goes wrong, he says.
Sign up today and you will receive a free copy of our Future Focus 2025 report - the leading guidance on AI, cybersecurity and other IT challenges as per 700+ senior executives
"Moving all the manufacturing from North America or Europe eastwards means you still have to ship everything back," Mohamad says. "Globalization has impacts, and when calamities or issues come up, everyone looks for localized support."
However, he believes that many organizations have pivoted or begun to pivot from a "complete focus" on maximizing efficiency and rebalancing by increasing flexibility and preparedness. Some already use AI and ML for predictive forecasting and crisis management.
For instance, providing visibility and transparent communications to partners and customers of ongoing mitigation efforts, through data transparency, automation, and streamlined communication — a lesson Mohamad says ALE itself learned through the several years to 2023.
Applying this meant ALE often managed to deliver products even when supplies were tightest, partly through investing more in its inventory to compensate for component shortages from the outset, he says.
It's all about ensuring enough margin of error is built in to cover the unexpected, Mohamad emphasizes. This means businesses must do more than just build out the warehouses near them, focusing instead on shoring up a resilient web of suppliers and partners.
Emile Naus, partner at consultancy BearingPoint, broadly agrees, though he notes that a downturn from 2019 and into 2020 was predictable given the industry's usual five to seven-year cycle. On top of that, he adds, a major Chinese factory caught fire shortly befotre the pandemic.
"You can't predict everything, particularly if you look only for specific things," Naus says. "You need to understand what may happen, and you can't forecast events that are too rare."
Commit to broader planning and supply chain resilience
Enterprise planning must be broader, cross-functional, active, and ongoing, if the sector is to avoid future supply chain shocks. Across all aspects of their supply chain, leaders must examine diverse options and consider alternatives – no matter how much they trust their current options.
While that logic isn't new, more organizations still need to learn it. "What we are seeing is that bigger companies will do disaster recovery but usually on specific events, while smaller companies tend not to do it at all," adds Naus.
Sam Harris, principal consultant at procurement-focused Proxima, points out that planning more generally to have more resiliency and more redundancy can be leveraged to free up resources that can function as an emergency fund.
This should be a key strategy for more organizations. Not paying attention means potentially suffering from "rising scarcity, and rocketing prices,” for key components such as chipsets, Harris says.
RELATED WHITEPAPER
During the worst of the supply chain crisis, chip prices rose by as much as 20% as worldwide chip shortages entered a nadir that would drag on as a two-year shortage. At one point in 2021, US companies had fewer than five days’ supply of semiconductors, per data collected by the US Department of Commerce.
Indeed, the crisis spurred government interventions. The US CHIPS Act opened up $280 billion in funding for semiconductor production and research over the next decade, while the EU Chips Act is similarly intended to drive funding that will diversify supply chains. An example is the new Taiwan Semiconductor Manufacturing Corporation (TSMC) construction in Dresden, Germany.
At the end of 2023, the US government also announced a review of the semiconductor supply chain to reduce US corporate reliance on China with a specific focus on chip production.
“There are other areas of technology where there hasn't been that same focus," warns Harris. "In the UK there are plans in place, but as far as I know, little solid progress."
"Controllable" issues more or less ignored include the professional and IT services markets, with many countries including the UK hugely reliant on on services and talent from abroad, he says.
Tom Fairbairn, data specialist at software engineering firm Solace, says central banks now at least regularly examine supply chain issues when setting interest rates because those inflections affect inflation. Certainly, the criticality of supply chains has become more recognized from a general economic point of view.
"You've got the Biden administration for instance doing a lot around re-shoring, unique to semiconductors," Fairbairn agrees. "We talk about what happened in Covid, even pre-Covid, but going right back there was a lot of complacency right after the fall of the USSR around things like geopolitical risk."
Of course, the IT industry is only one player in macro shifts such as geopolitical upheaval, and climate change. For the industry to stand firm, it has to be primarily about more effective mitigation strategies, most of which take time to design and implement.
"Demographic shift is going to shift demand patterns, for instance," he says. "But people have realized there's a trade-off between security of supply versus cost."
Fairbairn contrasts the previous "just-in-time" standard, which saw companies still producing to demand without holding large volumes of inventory, with the current approach to holding larger stock to reduce risk. He notes that this also allows for better data to be kept on supply, giving customers and the wider industry greater visibility in the face of shortage risks, Fairbairn says.
More customizations can require more components with more individual features to create them, so Fairbairn notes that the concept of "infinite personalizations" may have to be unlearned when it comes to future digital transformation.
Instead, manufacturers could seek to invest in better data analytics operations and logistics management. AI/ML powered simulations and digital twinning may deliver needed visibility of contributory dynamics, Fairbairn adds.
"It's all about ensuring you have a better understanding on the ground as to what your next or your other options are if you can't get your perfect combination of bits and pieces," Fairbairn says. "And yes, everybody needs to be talking to everybody else about everything."
Fleur Doidge is a journalist with more than twenty years of experience, mainly writing features and news for B2B technology or business magazines and websites. She writes on a shifting assortment of topics, including the IT reseller channel, manufacturing, datacentre, cloud computing and communications. You can follow Fleur on Twitter.
-
Cloudflare is cracking down on AI web scrapers
News Cloudflare CEO Matthew Prince said AI companies have been "scraping content without limits" - now the company is cracking down.
-
Swiss government data published following supply chain attack – here’s what we know about the culprits
News Radix, a non-profit organization in the health promotion sector, supplies a number of federal offices, whose data has apparently been accessed.