Cut your losses: The CIO's guide to waste in IT
Waste in IT is real: Defects, overproduction, waiting, underutilized talent, transportation, inventory, motion, overprocessing, and extra processing hinder organizational advancement
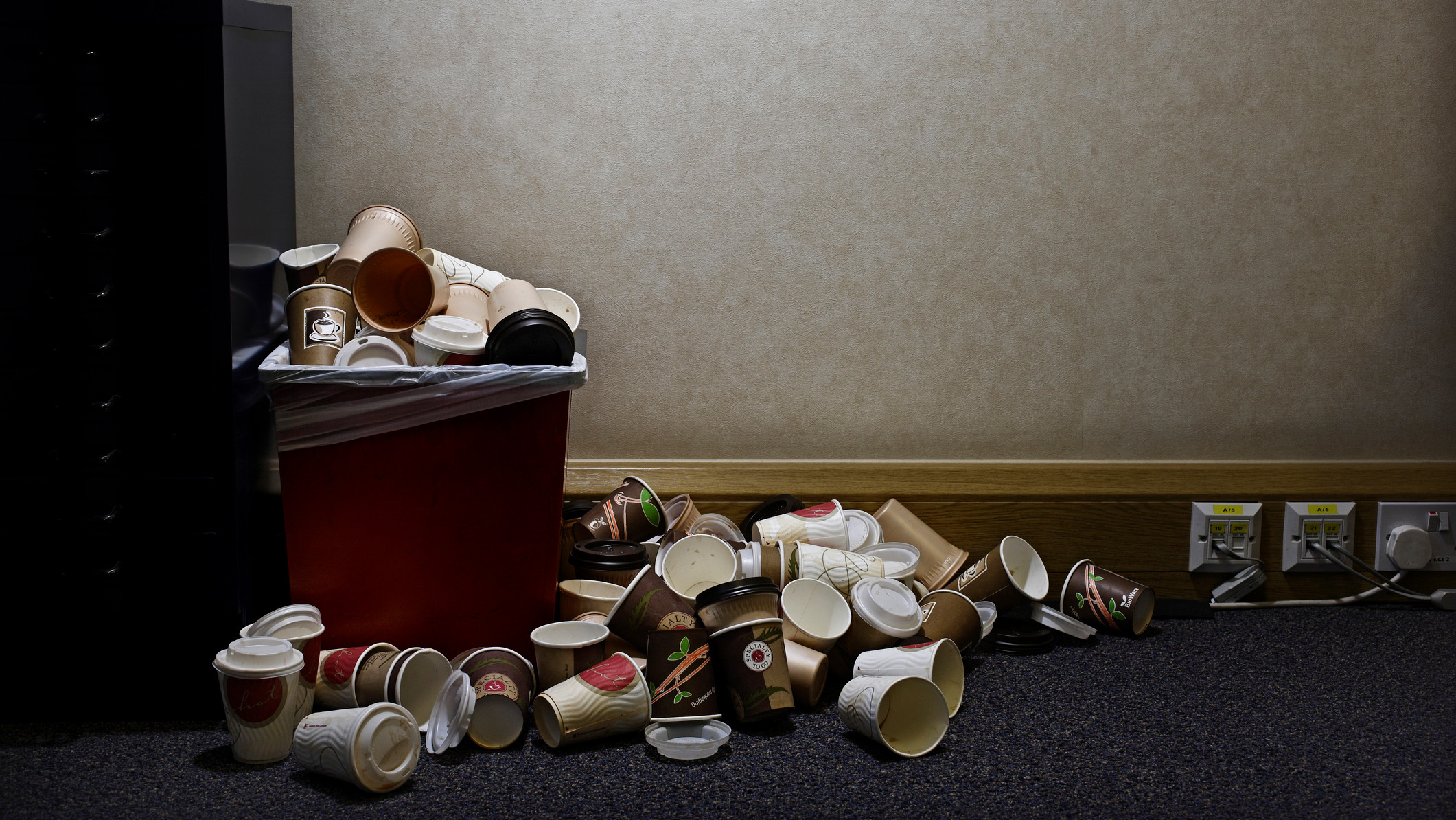
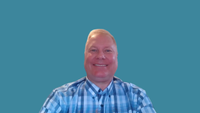
As a CIO, you are committed to smoothing operations by continuously improving services and processes. But what if I told you that removing waste from your IT processes is the key to significant improvements?
Eliminating waste is not just a task. It's a responsibility to foster a culture of continuous improvement. So, please put on your thinking caps, and let's explore how these Lean manufacturing principles can transform our IT departments.
The nine wastes of Lean: A quick primer
Before diving into the IT world, let's quickly review the nine wastes of Lean. While initially designed in the 1950s by Toyota for manufacturing, Lean and the concept of waste are surprisingly relevant in our digital world. While programmers have embraced the idea since the early 2000s, the rest of IT has lagged—time for CIOs to catch up and apply the concept of waste across your department and organization. The types of waste include:
- Defects: Errors requiring correction
- Overproduction: Making more than necessary
- Waiting: Idle time between operations
- Underutilized Talent: Waste of talent and imagination.
- Transportation: Moving of material or information not necessary
- Inventory: Excess stock or data
- Motion: Wasting motions in the process
- Overprocessing: More work than the job requires.
- Extra processing: Unnecessary activities not needed.
Let's evolve our understanding of those manufacturing concepts from the factory floor to the server room.
Now that we're viewing IT through the Lean and waste lenses let's apply these principles in a practical, actionable way to make our IT processes leaner than an IT department budget. Here are how the types of waste manifest themselves within the IT sector – and the actionable strategies you can confidently implement.
Defects: When good code goes bad
Equated to defective products in manufacturing, what does 'defect' mean to a CIO? Misconfigurations, data errors, and bug-ridden code cascade through your systems faster than a viral tweet. Consider a misconfigured firewall exposing your network. Maybe a database query returned erroneous results that had driven business decisions to go off on a tangent. As CIO, you are off the path and wasting time. Employees need to work to do the job correctly the first time. Every defect affects quality and reputation.
Overproduction: Too much of a good thing
Overproduction in IT doesn't often involve widgets. It does include producing reports that nobody will read or irrelevant features. It's that cluttered drawer in our homes with old phone chargers except detailed month closing reports that find their way to the digital dustbin. Another classic case is over-purchasing laptops for employees and having equipment aging on the shelves, which will soon be unusable in our ever-evolving IT landscape. It's like hosting a party, cooking too much food, and being left with much-wasted effort and stale hors d'oeuvres.
Sign up today and you will receive a free copy of our Future Focus 2025 report - the leading guidance on AI, cybersecurity and other IT challenges as per 700+ senior executives
Waiting: The spinning wheel of death
In manufacturing, one waste is waiting. IT has an overabundance, too: think slow load times, ponderous approval processes, or even that member of the team who always forgets to respond to messages. Imagine a painfully slow ticketing system with your IT support team thumb-twiddling while users fume. Time to speed things up. Alternatively, visualize a mission-critical software deployment buried under a highly complex or intricate approval process buried under a microscope for weeks. It's like watching paint dry, except it is made of your productivity and evaporates.
Unfulfilled potential: Diamonds in the rough
Unfulfilled potential is the waste that comes from underutilizing your team and wasting their talent on non-value-driven tasks. Paying a brilliant data scientist to update spreadsheets all day, or a network engineer who does UX design to fix printer jams is like hiring a Formula 1 driver to parallel park all day. As a CIO, employees are your greatest assets. Let's unleash the talent. Time to let your IT peacocks spread their feathers!
Transportation: Digital traffic jams
IT Transportation waste is about moving redundant information around or following some zigzag workflow to complete a simple task, which feels like running an obstacle course. Consider your team using email to send files back and forth instead of storing them in a shared location or using one of the best cloud file sharing servies: this is the ultimate example of waste in electronic transportation. Another example would be forcing users to input information into multiple systems, the equivalent of forcing someone to use three buses to travel a block, which would be inefficient and frustrating.
Inventory: Data hoarding gone wild
IT inventory waste shows up in many ways: unused licenses, obsolete hardware, or databases full of out-of-date information. It is the virtual version of the garage where you cannot park a car because it is full of stuff you might need someday. You bought 500 software licenses while having only 300 employees. Are those service-hosting servers still whirring away in the corner for services nobody has used since the last solar eclipse? It's time to hold that digital yard sale.
Motion: Digital dance to inefficiency
Undesired motion in IT involves all those extra clicks, swivel chair processes, or the equivalent of running around like a headless chicken. Perhaps a user interface requires more clicks than necessary to access a data point. Furthermore, printers or inventory might not be easily accessible. Think about how a support technician jumps back and forth between five applications to fix one ticket. That's like trying to cha-cha, robot, and moonwalk in one smooth move; impressive, yet highly inefficient.
Over-processing: Best laid plans
CIOs must never add more complexity to a service, task, or process than is necessary to get the desired value. Our team often over-engineered solutions to create complexity or generally applied bureaucratic processes that are unnecessary. We have all had software features added that no one used, such as a 20-step approval process for a simple software update or purchasing a business monitor – so it's important to remember that sometimes, less really is more. Alternatively, picture building a custom solution when an off-the-shelf product would be adequate. Don't use a sledgehammer to crack a nut.
Extra processing: The forgotten waste
Employees waste time. Is it true? Most Employees waste time not due to laziness but because they must follow leadership instructions. Holding them accountable for completing duties given unquestioningly by a supervisor is unjust. For instance, an employee who spends ten hours a week on a task to adhere to an old regulation that no longer needs to be followed is wasteful. This situation indicates that the system, not the employee, is at fault.
How often do you, as CIO, ask an employee why they complete a task? The employee usually responds, "Because that is how we have always done it." Even worse, no one understands the historical reason why. A fair question is whether we need to do it at all – can it be automated instead? If not, perhaps it's time to throw it in the garbage.
Ah-ha moment: Garbage out is value added
Here's the kicker, folks: removing these wastes is adding value. It's like decluttering your digital house – suddenly, you can breathe easier, move faster, and focus on what matters. By identifying and eliminating these wastes, you can cut costs, create space for innovation, improve user experience, and boost team morale. Bearing all this in mind can help leaders achieve a digital detox, leaving teams leaner, meaner, and ready to hit the next challenge.
RELATED WHITEPAPER
Lean IT doesn't mean doing more with less; it means doing more of what is right and less of what is wrong. That's creating a culture where everyone becomes competent and can find the waste to destroy.
So the next time you're leading or just sitting through a strategy meeting, instead of asking, "What can we add?" allow yourself to ask, "What can we take away?" You might just be surprised at the tremendous value you will create by removing the clutter. If you will excuse me, I have some redundant e-mails to delete and a ticketing system to rationalize. This war on waste isn't going to wait for any CIO.
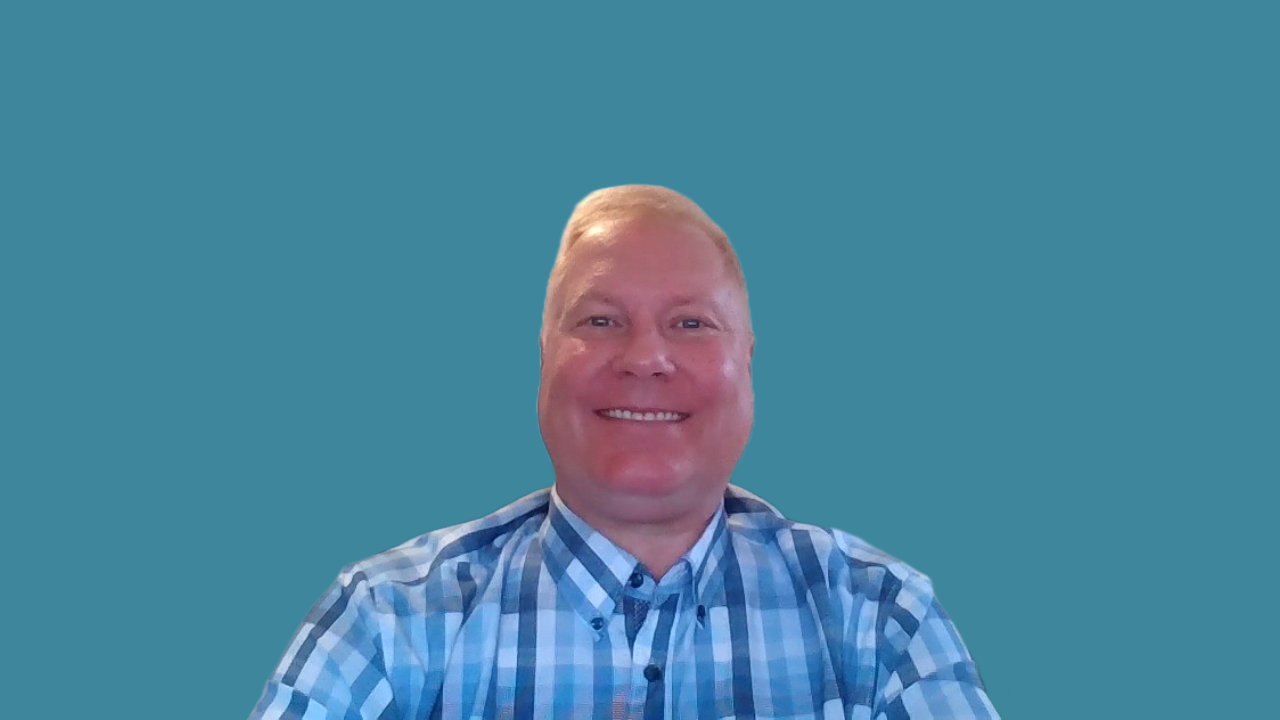
Dr. John Honchell is Future B2B's IT Industry Analyst. With almost three decades of experience as an IT leader with the roles of CIO and Global Lead, John has a passion for AI, Cyber Security, DevOps, Cloud, IT infrastructure, IT Innovation, and IT Automation.
-
AI coding tools are booming – and developers in this one country are by far the most frequent users
News AI coding tools are soaring in popularity worldwide, but developers in one particular country are among the most frequent users.
-
Cisco warns of critical flaw in Unified Communications Manager – so you better patch now
News While the bug doesn't appear to have been exploited in the wild, Cisco customers are advised to move fast to apply a patch