Is it cloudy in manufacturing?
The cloud may be a dominant presence across most sectors and businesses, manufacturing has been more hesitant
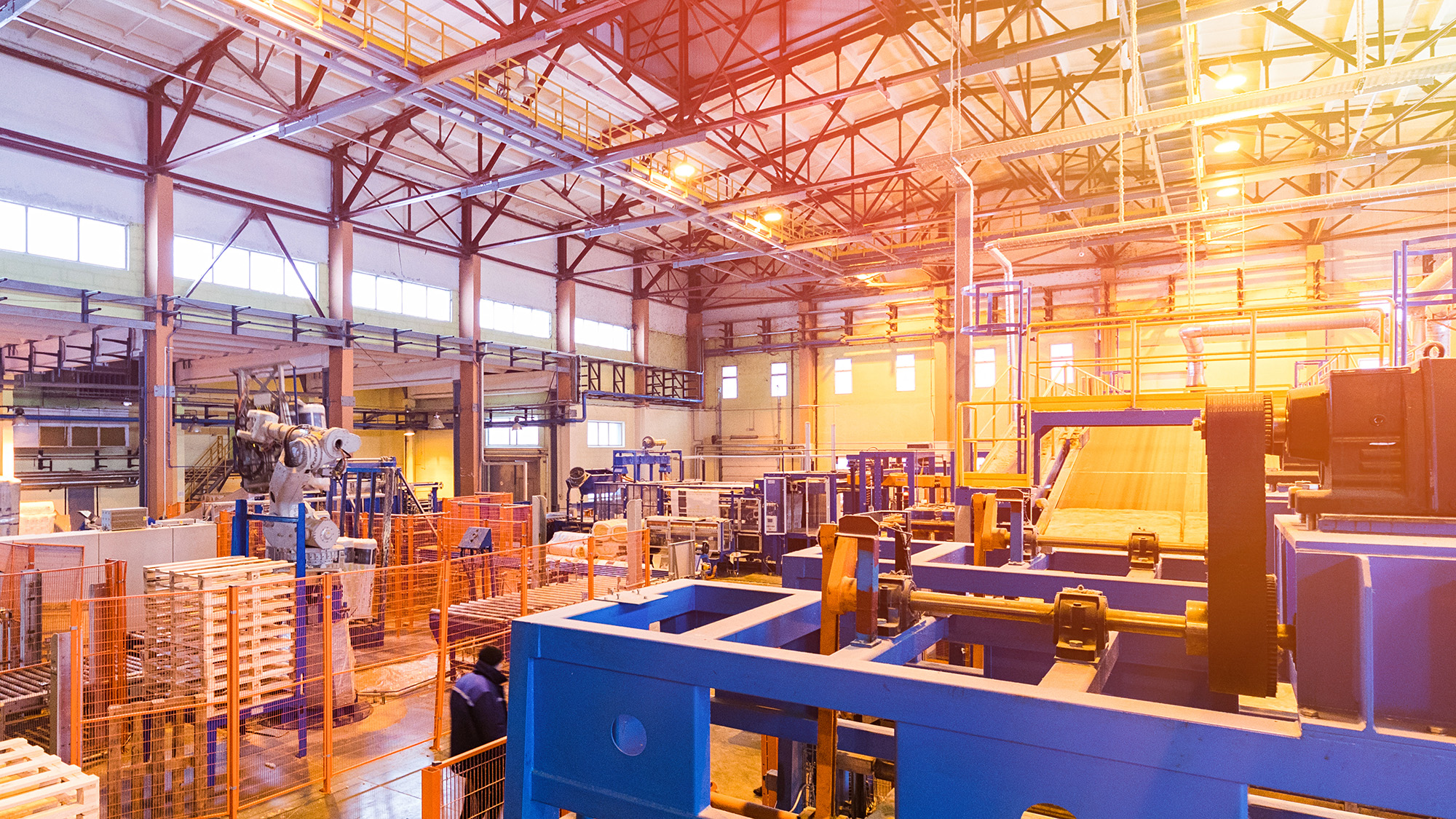
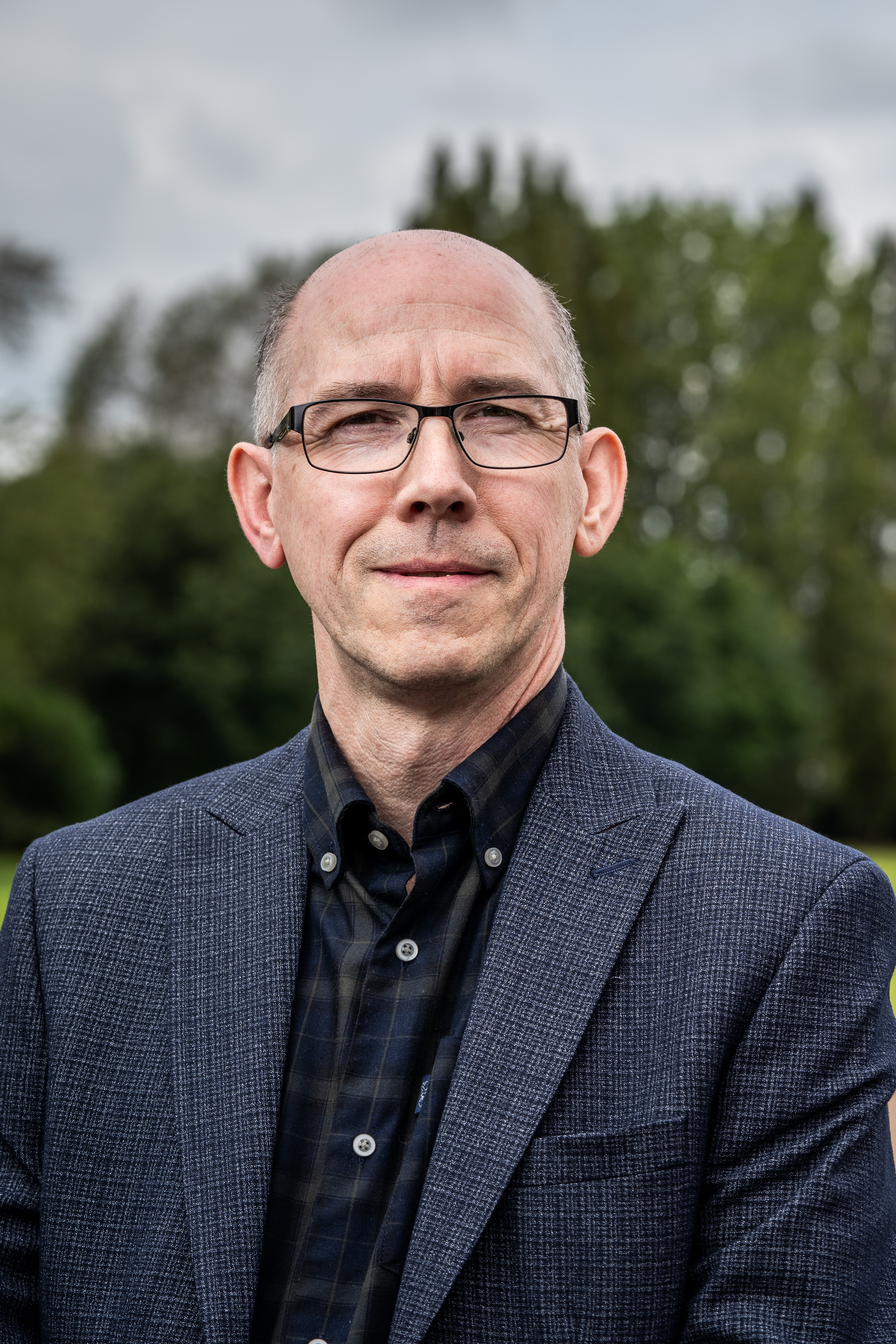
More than a quarter of IT directors in manufacturing are concerned about slow performance when running applications in the cloud, according to new research from label design and management software provider NiceLabel. However, eliminating issues around performance and legacy systems integration would spark a faster migration, with 50% ‘much more likely to move their applications to the cloud’ as a result.
How manufacturing approaches its use of cloud deployments will be subjective. As Rohit Gupta, senior product manager at Cognizant, tells IT Pro, some businesses are further along their cloud path than others: “Some manufacturers have taken Industry 4.0 very seriously and have made an effort to implement technologies at scale to adopt it. However, most manufacturers have taken Industry 4.0 one step at a time, first trying to prove the benefits of each technology they implement so they can scale up confidently further down the line. The era of scaling up will arrive when Industry 4.0 is truly realised but we’re not fully there yet.”
IoT and 5G will usher in a new level of connectivity all manufacturers can benefit from and cloud is an essential partner, albeit one that will need to be integrated with a range of new and legacy technologies.
The manufacturing cloud
In the past, manufacturing operations management (MOM) applications were deployed within a manufacturer's site. With little network capacity, businesses had a very insular approach. As Industry 4.0 continues to develop, and a new age of connectivity expands, MOM applications can move to the cloud, if this is viable.
Speaking to IT Pro, Maddie Walker, Industry X practice lead at Accenture UKI, explains that bringing manufacturers increasingly into cloud environments is the future of their businesses. “Firstly, Industry 4.0 has brought connectivity to the factory floor,” she says. “For example, you have market leaders using digital monitoring and maintenance technologies and automating processes to speed up decision making. You also have leading companies deploying full robotic automation in production. By embedding AI and analytics into operations, and evolving with robotics and digital twin technologies, manufacturers are augmenting their human workforces with technology and providing greater insights.”
Another critical trend is composable IT architectures and how they connect with cloud and hybrid data centre deployments that might be in place. “By identifying available resource pools, the IT architecture will be able to assess, review and determine the availability and utilisation of all IT resource pools – ensuring that there is compute and storage space for operations,” explains Andreas Rindler, managing director at consultancy firm BCG Platinion. “Meanwhile, dynamic resource sharing will mean that the architecture can optimise the utilisation and provisioning of the right resources where and when needed, speeding up processes.”
And the use of digital twins is also expected to expand across manufacturing rapidly. Estimates from Juniper Research put spending on digital twin technologies to be over a third (34%) of total spending by manufacturers this year.
Get the ITPro daily newsletter
Sign up today and you will receive a free copy of our Future Focus 2025 report - the leading guidance on AI, cybersecurity and other IT challenges as per 700+ senior executives
Smart manufacturing
The creation of the smart factory has been a long time coming. Today several technologies are converging to make the manufacturing landscape more intelligent.
Walker explains that data and analytics are at the core of the smart factory: “Combining IoT with data analytics tools on the cloud allows manufacturers to receive key information at pace and provides them with a detailed picture of where efficiencies can be made across their suite of smart manufacturing products. It’s these insights that allow factories to be ‘smart’ – by linking humans, machines, and products across the value chain and decisions can be made quickly.”
Even with a range of mature and semi-mature technologies available, the manufacturing space can seem sluggish compared to other sectors or industries. Mark Yeeles, vice president of industrial automation at Schneider Electric UK&I, believes the slow pace of digitisation is not entirely the manufacturers' fault. “Most accounts, several digitisation efforts have yet to achieve their anticipated benefits,” he says. “However, we can't place all the blame on the technology for not reaching its full potential. The technology is there – frequently, the complexities that operate within running a business or factory that hold it back.
“For example, many factories and the automation machinery within them aren’t always brand new, made by a singular brand and interconnected by a cutting-edge operating system. Embracing this fact and helping customers to connect by using [technologies] such as the Cloud can help them to scale up and garner greater intelligence to make better business decisions and improve operational efficiency.”
There is little doubt that the cloud will have a profound and long-lasting impact on every aspect of manufacturing. As Gupta says, the future is cloudy: "The era of scaling up will arrive when Industry 4.0 is truly realised but we’re not fully there yet. The number of manufacturers currently using cloud in any sophisticated way is minimal because the industry has been slower to keep up with the digital world. However, this will very quickly change as the adoption rate of cloud in manufacturing is staggering - 94% of companies already use a cloud service in some form (according to Flexera). This tells us that there is a lot more to come, and soon, so watch this space.”
Manufacturers can see that the cloud will underpin their businesses, but cost and updating legacy systems are slowing the adoption of Industry 4.0. However, investments must be made to take advantage of the range of technologies integrated to create a smart factory.
RELATED RESOURCE
Cloud operational excellence
Everything you need to know about optimising your cloud operations
Eric Stoop, CEO of manufacturing software specialist EASE, implores leaders across manufacturing businesses to embrace the cloud now: “While this is understandable, especially as the pandemic continues, history shows us that those who take action in difficult times come out the other side stronger. Manufacturers should view any cloud technology spend as an investment in future profitability rather than a cost that impacts the bottom line in the short term. “
5G, IoT, AR and AI will all influence how a factory will operate not in the distant future but tomorrow. The manufacturing space has a range of new technologies to deploy. The hesitancy evident in some quarters is understandable as any change in the manufacturing industry has always been traditionally slower than in other sectors. However, change is accelerating and manufacturers who can embrace the new technologies and integrate them seamlessly will create next-generation factories.
David Howell is a freelance writer, journalist, broadcaster and content creator helping enterprises communicate.
Focussing on business and technology, he has a particular interest in how enterprises are using technology to connect with their customers using AI, VR and mobile innovation.
His work over the past 30 years has appeared in the national press and a diverse range of business and technology publications. You can follow David on LinkedIn.
-
CISA issues warning in wake of Oracle cloud credentials leak
News The security agency has published guidance for enterprises at risk
By Ross Kelly
-
Reports: White House mulling DeepSeek ban amid investigation
News Nvidia is caught up in US-China AI battle, but Huang still visits DeepSeek in Beijing
By Nicole Kobie