The exciting future of digital twinning
The channel is perfectly poised to exploit a rising demand for robust testing, says Abel Smit
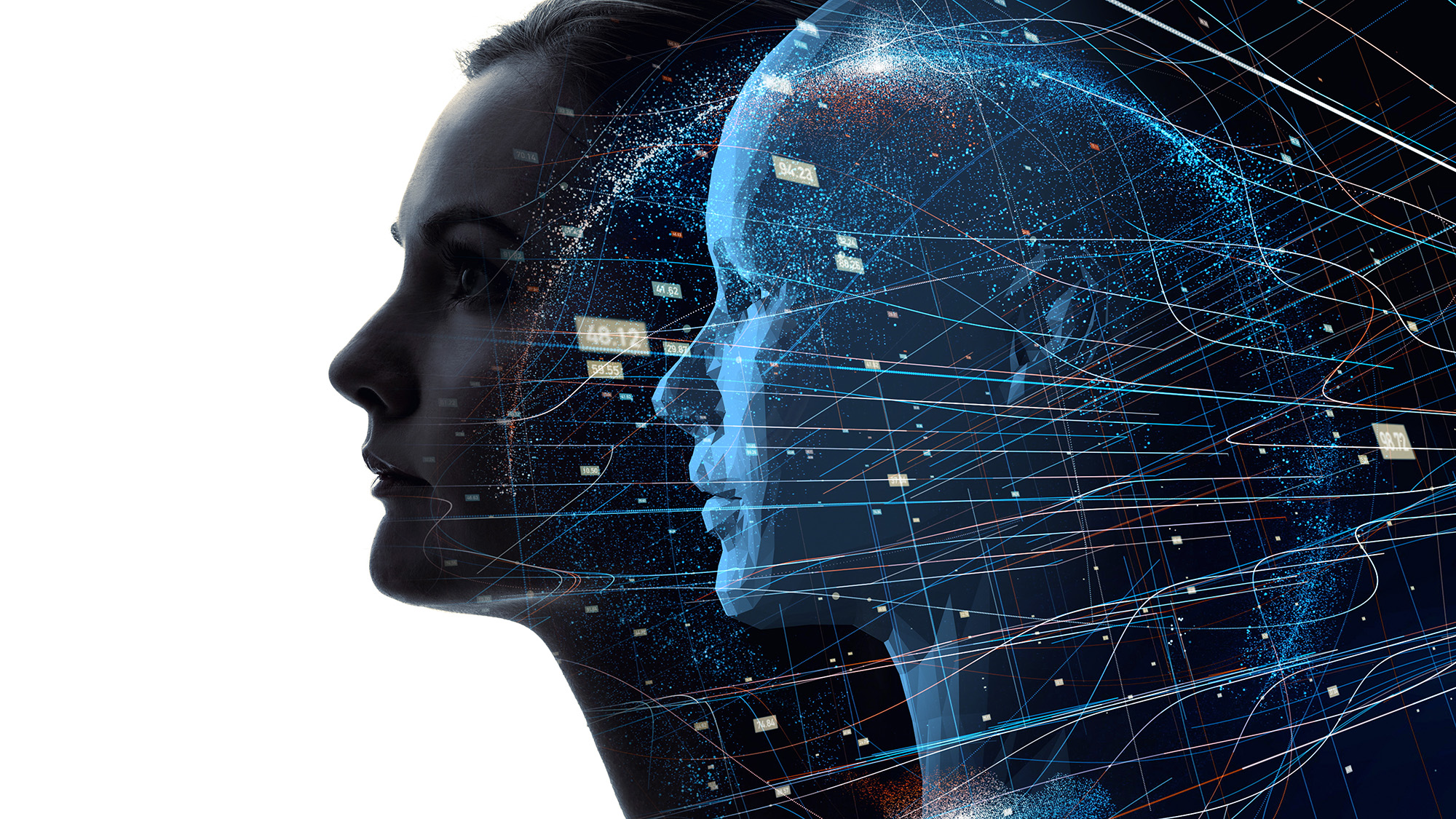
Digital twinning was once thought of as revolutionary technology, exclusively used for high-value projects and products. Now, it's being used to tackle more everyday manufacturing problems and is poised to become more commonplace across numerous other sectors.
Digital twinning involves taking a physical asset and creating an exact copy of that asset in the digital world. Using data from sensors attached to the physical asset, organisations can analyse its efficiency, errors or anomalies, to improve and optimise performance, and understand the condition of the asset in real-time.
With a model that is both digital and dynamic, businesses can accurately conduct tests on how the physical version will perform in the real world, across the duration of its lifecycle. The clear advantage of digital twinning for businesses is the ability to experiment in the digital world much less destructively, at large scale.
Organisations have already adopted digital twinning in the "make" industry for product design and machine design but also in the building industry. In the building industry, for example, it's particularly useful for architects, contractors, operators and owners to model and emulate the entire lifecycle of a building before it is even starting to be built.
Having a digital twin of building projects is becoming increasingly prevalent. For instance, the new £15-billion Crossrail project -- the construction of a new high frequency, high capacity railway for London and the South East of England - has its own digital twin. You can use a computer model and computer generated tests to learn about the behaviour, optimize designs and minimize waste.
As computing power has become ubiquitous, the number of scenarios and alternatives you can analyse are endless. This type of synthetic learning will result in a better-built environment.
Historically, design components did not have any machine intelligence of their own. Businesses had no means of establishing how changes to different elements or environmental factors impacted overall behaviours within a design. Digital twinning relies on mountains of analytics and open federated data, and continuously learns and updates itself from multiple sources, to represent its near real-time status, working condition or position.
ChannelPro Newsletter
Stay up to date with the latest Channel industry news and analysis with our twice-weekly newsletter
A digital twin can also be used for monitoring diagnostics and prognostics to optimise asset performance and utilisation. Here, sensor data can be combined with historical data, human expertise and fleet and simulation learning, to improve the outcome of prognostics. The goal is to gain insights into the behaviour and performance of physical objects, by exploring them in more detail via a digital representation.
As part of what has been dubbed "the fourth industrial revolution" (or Industry 4.0), this form of machine learning will hugely impact the manufacturing landscape, with 85% of Internet -of-Things-enabled platforms having digital twin functionality within the next five years, according to a recent global report conducted by Research and Markets.
Teams put in place to manually maintain these assets in the past will now be less vulnerable to an unplanned failure or crisis and will, instead, have more time to make changes rather than conducting checks on the asset in person.
Channel partners with a value-added sales approach understand what it takes to work with IT or IP- based technology across many industries, thus, digital twinning represents an enormous opportunity for 2018 and beyond.
It pushes out the technology envelope and embodies a far more sophisticated way to understand behaviours of the physical world. Those who understand how to connect the virtual and the physical worlds are perfectly placed to exploit a growing demand for this tech going forward.
Abel Smit is IoT consulting and customer success director at Tech Data Europe
-
Cleo attack victim list grows as Hertz confirms customer data stolen
News Hertz has confirmed it suffered a data breach as a result of the Cleo zero-day vulnerability in late 2024, with the car rental giant warning that customer data was stolen.
By Ross Kelly
-
Lateral moves in tech: Why leaders should support employee mobility
In-depth Encouraging staff to switch roles can have long-term benefits for skills in the tech sector
By Keri Allan