Short circuit: Will the chip shortage end this year?
With tech remaining in short supply, we explore whether the industry can get supply chains up and running any time soon
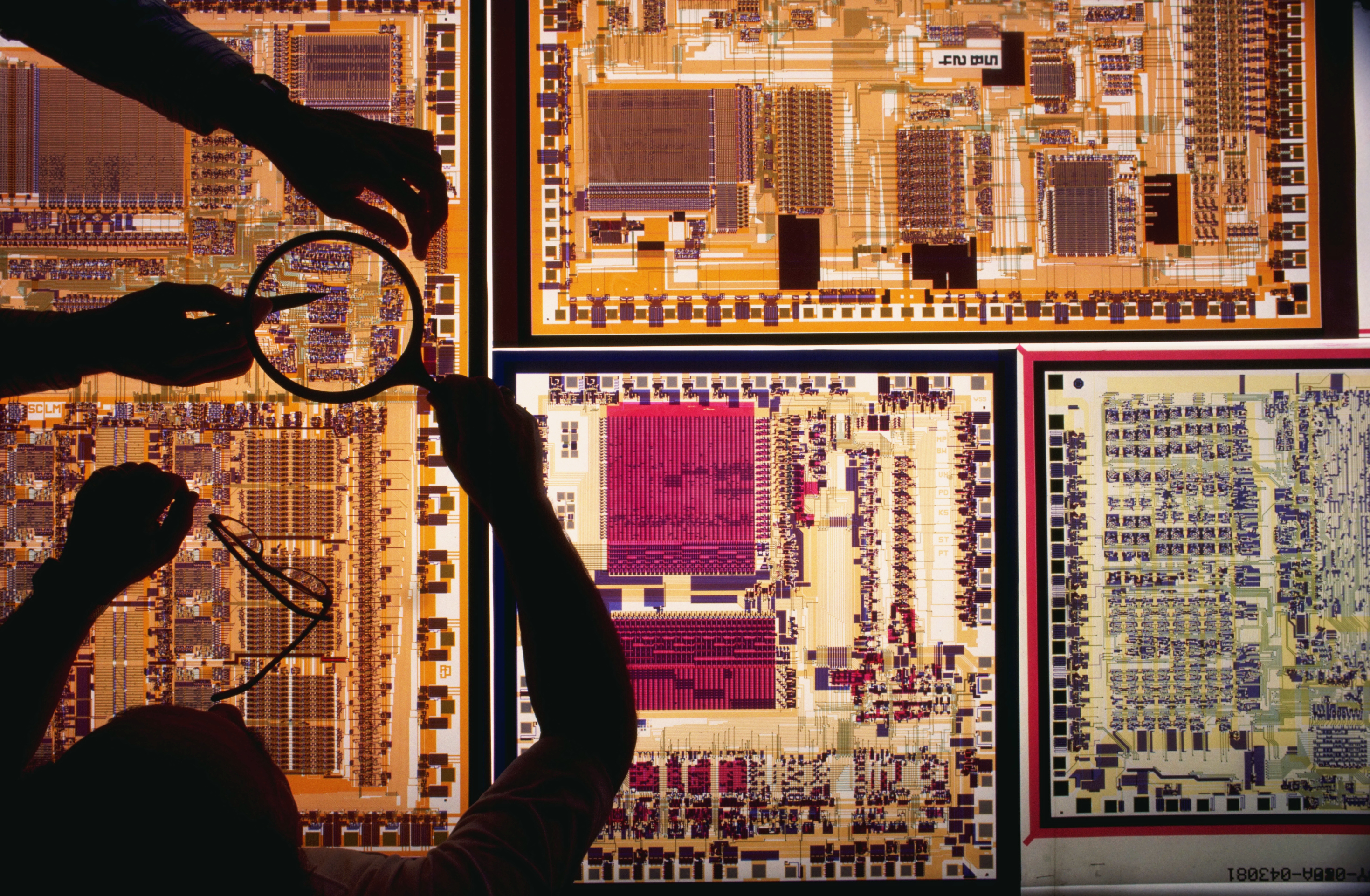
If you’ve bought any new computing equipment over the past couple of years then congratulations – it can’t have been easy. From phones and games consoles, to graphics cards and networking gear, the entire industry has been throttled by the ongoing shortage of semiconductors.
Even the biggest companies have been hit – last year, Apple was forced to scale back manufacturing plans for the iPhone, and more than a year after launch it is still virtually impossible for consumers to buy a PlayStation 5.
Is there any sign of things returning to business as normal or should we expect shortages for the foreseeable future?
A big problem for small companies
“If you can't build PlayStations or iPhones, we don't stand a chance,” laughs Sue Ballard, the customer support manager at Offshore Electronics, a contract manufacturing firm in Guernsey. It makes the digital guts for everything from cat-flaps and escalators, to critical hospital equipment, such as power supply units and even ventilators.
“Our efficiencies have gone down the pan,” says Ballard. “We're doing the same job five times over, we've had to change quite a lot of our processes. We're a different company.”
The problem Offshore faces is a severe shortage of components, as one missing piece can cause a knock-on and delay the entire manufacturing process. But the crisis has caused other stresses on the business too.
“Normally you place one purchase order and it's done, the bits come in, you pay it and you don't have to worry about it,” says Dan Attewell, the company’s technical sales director. “But, at the moment, if that stock doesn't come in we've got to go and buy some more. So, you’ve got to raise two purchase orders and you've got to pay two suppliers to get the same amount of bits.”
ChannelPro Newsletter
Stay up to date with the latest Channel industry news and analysis with our twice-weekly newsletter
Even if supplies eventually arrive, it creates chaos for scheduling. “We buy all of the parts in for the month before [the finished item] is due to the customer,” says Attewell. “So we've got a manufacturing window of, say, four weeks. But we might not have all of the bits now until the week before the product's due. Your window gets shorter and your planning is worse, and you then have this massive peak of everything all at once. It's great that we're so busy, but it's an absolute nightmare.”
According to Ballard, it is particularly chaotic because suppliers will often “decommit” at short notice and not deliver what they had promised. It’s a well-known phenomenon in economics known as the ‘bullwhip effect’.
“Information gets distorted and people start to play games with their orders,” says John Fowler, an Arizona State University professor and Motorola professor of supply chain management. “People may order twice as much as they need knowing they're going to get their order cut. And so this whole distortion of information moves all the way back through the chain, which causes the people that are at the very end of the supply chain to get whipped around.”
It’s more than the COVID-19 pandemic
Unsurprisingly, the most significant factor behind the shortages is, of course, the COVID-19 pandemic. “Demand for computers at home increased greatly because people were now working from home and needed to upgrade their equipment,” says Fowler.
RELATED RESOURCE
It wasn’t just our changing work habits, though, as the policy response of governments around the world had consequences too. “Almost all of the shutdowns came with some form of salary support, some some form of the government giving you money to just take it easy, which meant that unlike any other sort of recession, money was not in short supply,” says Hamza Mudassir, a visiting fellow in strategy at the Judge Business School at Cambridge and co-founder of tech consultancy Platypodes.
A spike in demand was not helped by a shortage on the supply side too, both due to COVID-19 restrictions in countries such as Malaysia, and the need to divert resources elsewhere. “It turns out that the same silicon that is used for semiconductors is also used to make vials for vaccines,” says Fowler. “So that drove up the price for the silicon.”
The pandemic isn’t solely to blame. Another factor is that some of the world’s largest chip suppliers have fallen victim to a series of unfortunate disasters. “There was a plant in Japan owned by a company called Renesas that caught fire,” says Stephane Crosnier, supply chain and operations lead at consultancy firm Accenture. “This plant was supplying about 30% of the worldwide capacity for [some] specific chips.”
Similarly, during 2020, another major fire hit the Unimicron plant in Taiwan, which produces the substrate used to make chips, and a prolonged power outage in Texas shut down major chip foundries around Austin, which are major producers of the wafer on which integrated circuits are printed. “If we hadn't had the pandemic, there was enough shock absorption in the system to handle those incidents, but when it was already on the edge, those things just made it that much worse,” says Fowler.
Slipping back to normality
Given the lack of supply and the enormous demand, the next question is obvious: can’t more chip foundries be built?
“The problem that comes with high-end semiconductors is that they are notoriously difficult to make,” says Mudassir. “The latest Intel processors, the new PlayStation, the new Xbox Series were all designed in a 7nm process that can only be done by a handful of companies in the world.
“The foundries where the semiconductors are built are very, very hard to actually build. It can take billions of dollars and three to four years for you to get to a point where a 7nm or a 4nm foundry is fully functional and running at capacity.”
Mudassir is optimistic that there will be good news – eventually. “Now what we have is a block of time that everybody is stuck in,” he said. “Foundries are being invested in, people are being trained, everybody's working their hardest, but the actual laws of physics are going to prevent you from getting a foundry up and running until there's a major technological breakthrough.”
Consequently, you shouldn’t expect a return to normal buying patterns anytime soon. “When you look at what companies are saying in this space, I think they still expect 2022 to be very, very difficult and are starting to say they're probably not expecting any back to normal before 2023,” says Crosnier, who also warns that further COVID-19 developments, such as a major outbreak in China, could continue to cause problems.
This is in line with what Offshore Electronics are expecting too, though there is clearly still a lot of uncertainty. “I think we're probably still maybe another year away from seeing that really come to fruition,” says Attewell. “We're seeing little glimmers here and there. We're looking for bits every day and [sometimes] someone would decommit us, and the next thing you know the truck turns up here and we've got loads of bits. And even the supplier didn't know they were coming in.”
In fact, fixing the chaotic information environment could be what helps fix the chip supply chains – and make them more resilient. “We are advocating what we call the creation of a supply chain stress test,” says Crosnier.
RELATED RESOURCE
Delivering on demand: Momentum builds toward flexible IT
A modern digital workplace strategy
“You may remember that on the back of the financial crisis in 2008, financial institutions had to undergo financial stress tests to prepare for that, so we are developing something very similar for companies to be able to first get a measurement of their supply chain resilience and, second, identify their point of weaknesses in supply chains.”
In the meantime, there is cause for optimism. Even though it may take some time there is light at the end of the tunnel. “We may very well, in 2023, go from having a shortage of chips to having more capacity than is needed,” says Fowler. “Because when you build a factory, these days, a modern factory can produce a tremendous amount of chips. Intel is building a factory. TSMC is building several new factories, Samsung is building new factories. So you've got a lot of capacity that is going to come online in 2023.”
-
Bigger salaries, more burnout: Is the CISO role in crisis?
In-depth CISOs are more stressed than ever before – but why is this and what can be done?
By Kate O'Flaherty Published
-
Cheap cyber crime kits can be bought on the dark web for less than $25
News Research from NordVPN shows phishing kits are now widely available on the dark web and via messaging apps like Telegram, and are often selling for less than $25.
By Emma Woollacott Published
-
Raspberry Pi CEO Eben Upton on surviving the semiconductor crisis
Case Studies The Raspberry Pi chief reveals how the organisation overcame component shortages during the COVID-19 years
By James O'Malley Published
-
What 2023 will mean for the industry
Whitepaper What do most IT decision makers really think will be the important trends and challenges in the coming year?
By ITPro Published
-
Podcast transcript: Solving the semiconductor shortage
IT Pro Podcast Read the full transcript for this episode of the IT Pro Podcast
By IT Pro Published
-
The IT Pro Podcast: Solving the semiconductor shortage
IT Pro Podcast When the chips are down, supply chains may need a long time to ramp back up to full capacity
By IT Pro Published
-
Intel suspends operations in Russia
News The move comes 34 days after Intel joined AMD in halting chip sales to Russia
By Sabina Weston Published
-
AMD announces Ryzen 5800X3D will ship in April
News AMD's flagsip V-Cache processor will offer a 15% performance bump over non-3D rivals, says chipmaker
By Danny Bradbury Published
-
Intel to invest €33 billion in EU chip manufacturing
News This will include the long-rumoured €17 billion semiconductor fab mega-site in Magdeburg, Germany
By Sabina Weston Published
-
AMD, Intel and TSMC reportedly block chip sales to Russia
News The move represents a potentially significant threat to a country with limited domestic production capacity.
By Danny Bradbury Published