What is 3D printing?
A handy explainer on the technology, use cases, and potential of 3D printing
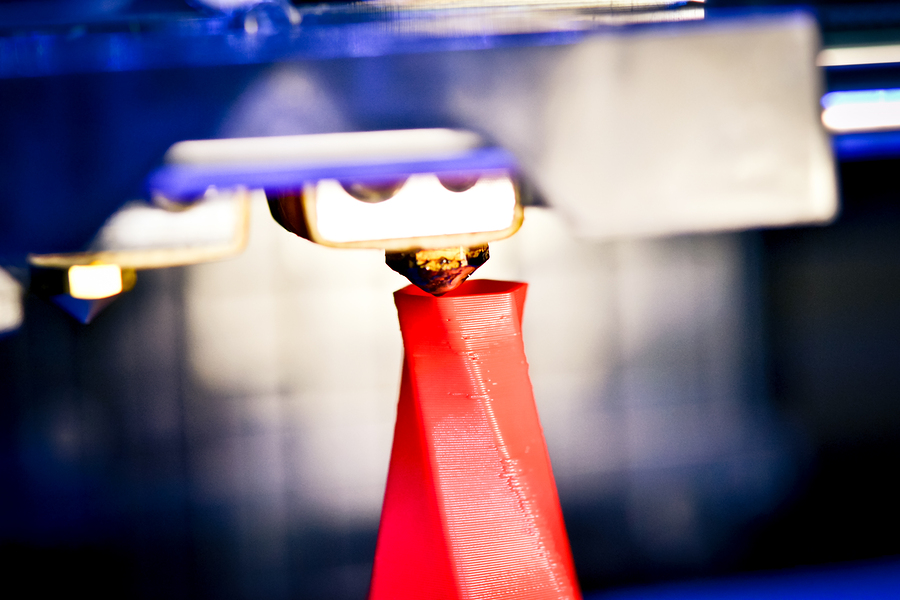
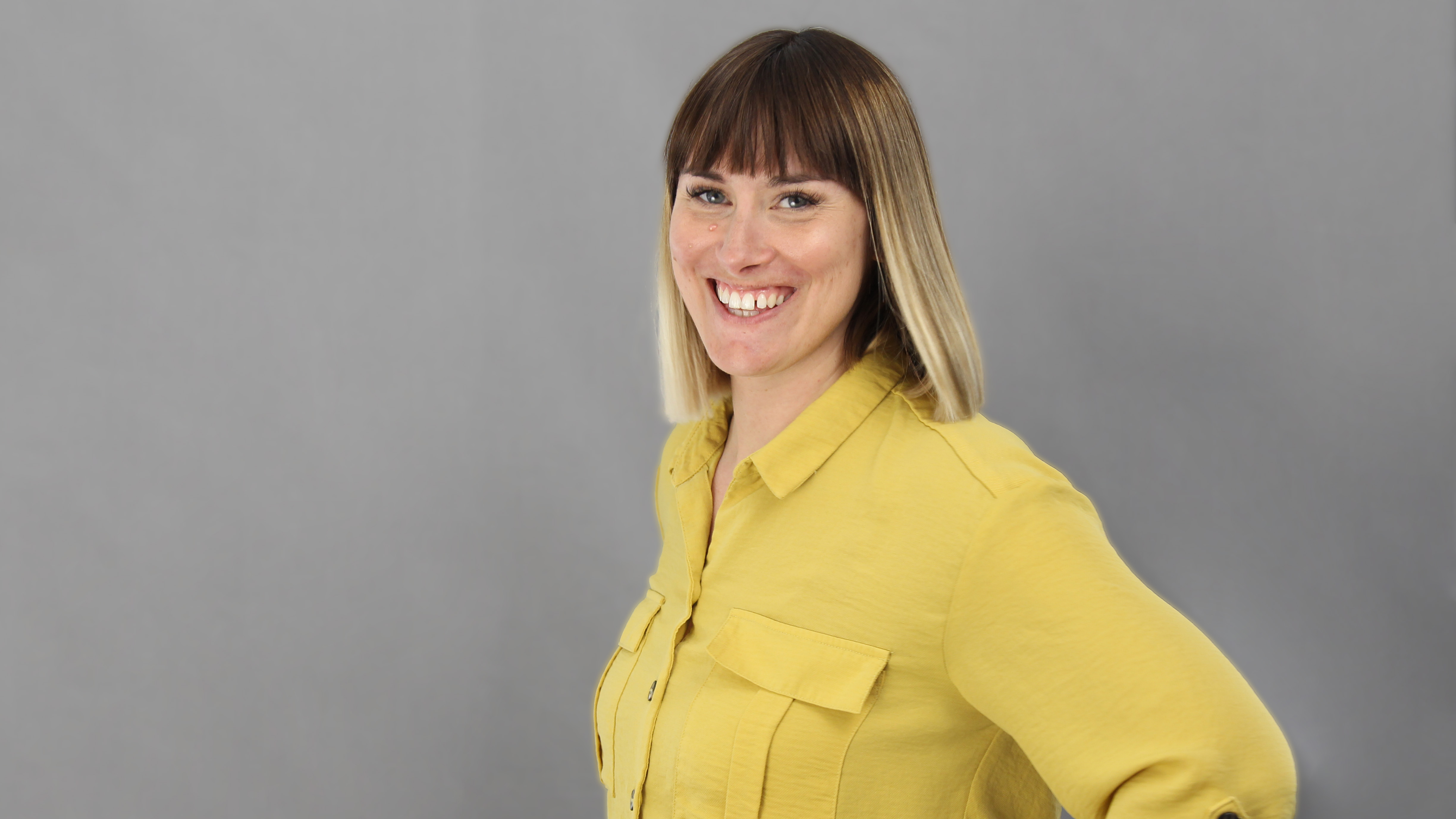
Over the last few years, 3D printing has become an increasingly popular manufacturing method to mass produce goods and also provide a way for hobbyists to stretch their creativity.
What is 3D printing?
As the name suggests, rather than being used solely for printing flat documents, it's used for creating 3D physical objects, building up an item layer-by-layer, with each layer of a toner-like substance building up to create a 3D object.
The process of building up an item using printed layers is known as additive'. The main advantage of manufacturing objects or components using additive is that it only uses the materials needed to create physical objects, rather than using large chunks of metal, plastic or wood, which create vast amounts of wastage, however careful manufacturers are when creating manufacturing templates.
The ink' used to create the objects varies from industry to industry. Metal powders, plastics, metal alloys, sandstone, rubber and even organic matter can all be used to create 3D printed objects, however large or small.
The majority of desktop or small-scale 3D printers use plastic toners, which are melted down and then applied to a printing surface, etched layer-by-layer, to build the design up into a physical item.
Is it popular?
Although 3D printing remains some way off becoming an everyday process, the technology is more than a passing fad. More than 278,000 3D printers were sold in 2015, almost double that of the previous year, according to Wohlers Report figures. In the last two years alone, sales of 3D printers have grown by 99%.
The additive manufacturing industry has grown 25.9% over the past year, generating over $5.2 billion in revenue. The total number of 3D printers sold may seem relatively low, yet because of the current high entry cost of the tech, most of these are within large companies and well-funded startups.
Get the ITPro daily newsletter
Sign up today and you will receive a free copy of our Future Focus 2025 report - the leading guidance on AI, cybersecurity and other IT challenges as per 700+ senior executives
Where is it used?
So far, the technology's biggest successes have been in industrial applications. It is extensively used in car manufacturing, particularly higher end prototype products or Formula 1 racing, where its customisability is seen as a strength.
Aerospace pioneer SpaceX is able to create engine parts using 3D printing without the substantial lead times that traditional processes place on deployment, speeding up the process dramatically.
And the field of architecture has been transformed through the use of 3D printing, where individual architects can create scale models directly from their own CAD designs, instead of using artists.
Engineers, prosthetic designers, shoemakers, and even drone hobbyists are taking advantage of the flexibility that 3D printing affords.
What are its benefits?
As the finished product is 3D, the technology allows designers to create complex shapes and intricate parts that would otherwise be too delicate to produce conventionally. Complexity in design adds no extra cost to additive processes, making it possible to work around current limitations.
Printing schematics act like normal files, which can be shared between computers and printers. So long as you have the correct toner to create the item, the printer files, such as spare product parts, can be downloaded from websites and sent straight to the printer.
The entire process is also highly cost-effective, which is particularly useful for startup businesses looking to prototype new designs on small product runs. Design changes can all be done within the schematic, avoiding the need to contact manufacturing plants to adjust the blueprint.
What are its drawbacks?
Most drawbacks are due to the infancy of the technology. Although the list is expanding, you are currently restricted in your choice of materials and colours. Most consumer parts are printed in greys or whites before being painted by the user, and the finished products lack the strength associated with traditional manufacturing.
Precision is also somewhat limited, as 3D printing is unable to produce the wafer-thin designs that some products require.
All pictures: Bigstock
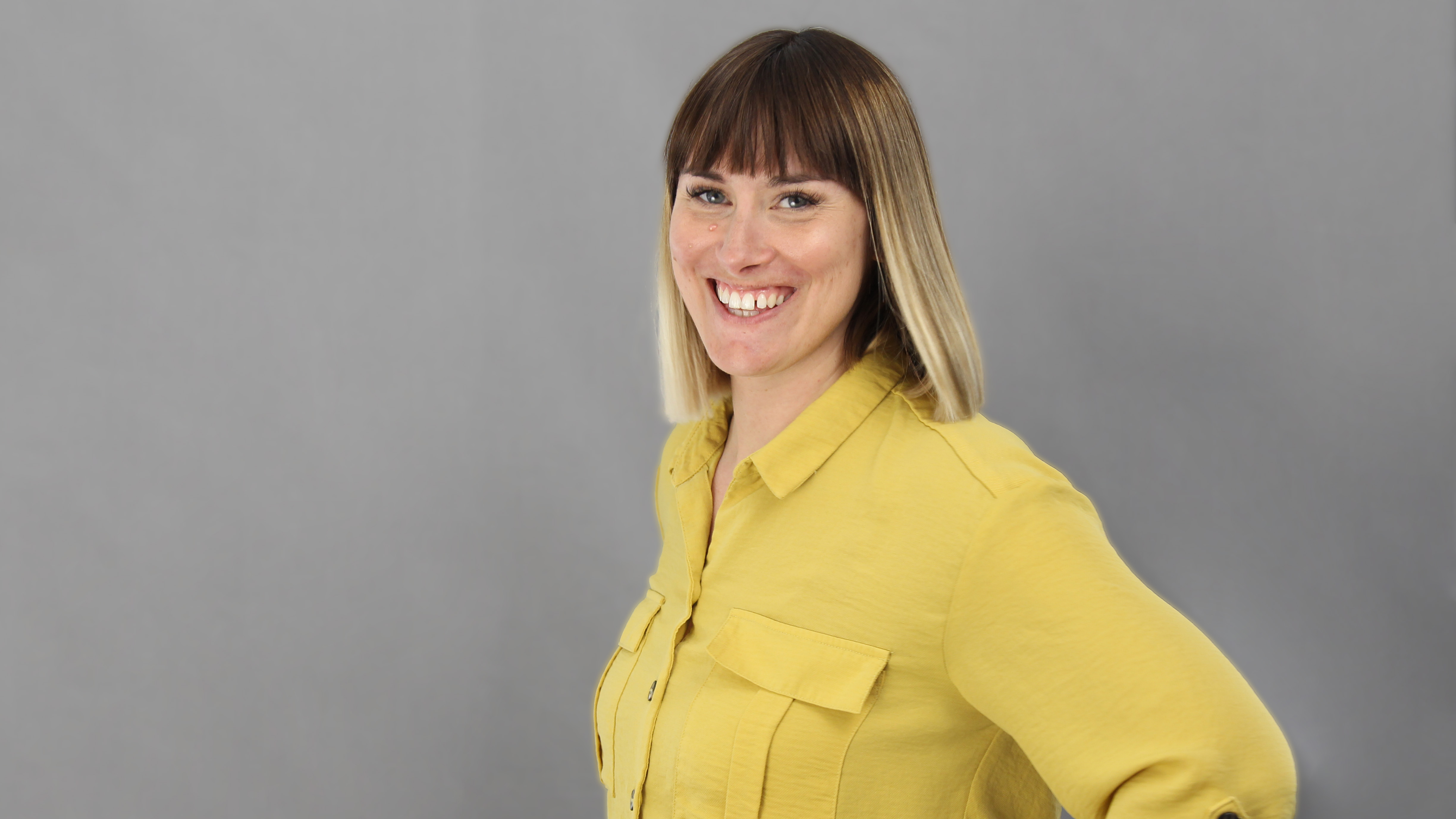
Clare is the founder of Blue Cactus Digital, a digital marketing company that helps ethical and sustainability-focused businesses grow their customer base.
Prior to becoming a marketer, Clare was a journalist, working at a range of mobile device-focused outlets including Know Your Mobile before moving into freelance life.
As a freelance writer, she drew on her expertise in mobility to write features and guides for ITPro, as well as regularly writing news stories on a wide range of topics.
-
Should AI PCs be part of your next hardware refresh?
AI PCs are fast becoming a business staple and a surefire way to future-proof your business
By Bobby Hellard
-
Westcon-Comstor and Vectra AI launch brace of new channel initiatives
News Westcon-Comstor and Vectra AI have announced the launch of two new channel growth initiatives focused on the managed security service provider (MSSP) space and AWS Marketplace.
By Daniel Todd